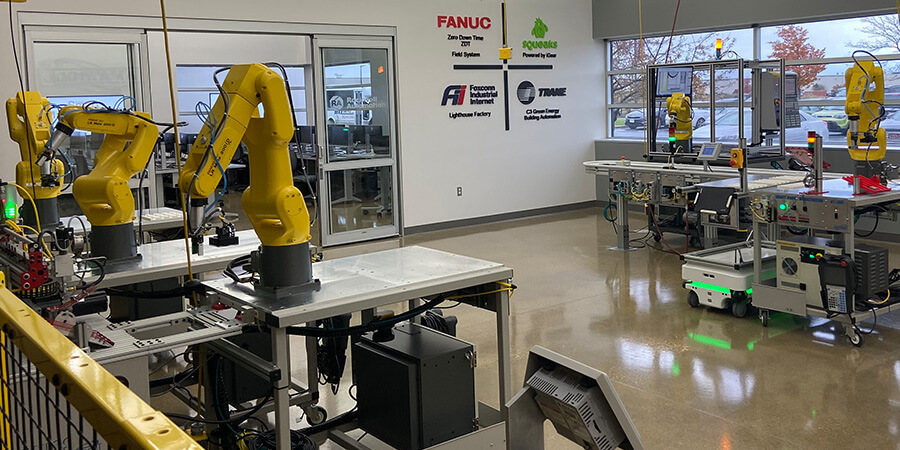
FANUC America’s effort to develop the next-gen manufacturing workforce from diversified areas and backgrounds will help fill the need for qualified candidates.
For the last 10 years, FANUC America has been building a framework across the U.S. to train the next generation of manufacturers, and demand continues to ramp up. In the wake of the COVID-19 pandemic, the industry is learning lessons about the global shutdown and its effect on the ability to get materials, products and goods.
“COVID really exposed a lot of vulnerabilities within our supply chain and the logistics of material goods, especially in the areas of food and beverage, fulfillment and distribution, as well as in the production of medical devices and PPEs,” says Paul Aiello, Executive Director of Education for FANUC America.
The notion of reshoring manufacturing in the U.S. isn’t a new concept, but the topic has gained steam in the last year. Many businesses are rethinking about what we produce and do not produce in this country.
“What we’ve seen in the last year is these really essential manufacturing sectors have committed to reshoring a lot of those operations within the U.S., they’ve committed to adding a lot of automation,” says Aiello. “In order to rapidly ramp up production, we’ve seen that they are investing more in automation as well as expanding.”
If businesses continue to add more automation and expand their advanced automation capabilities, then the demand for people with high-tech skills will continue to grow.
In the wake of the COVID-19 pandemic, the industry is learning lessons about the global shutdown and its effect on the ability to get materials, products and goods.
“We already have a tremendous skills gap in manufacturing, this expansion in vital sectors within the U.S. supply chain will only stress that skills gap even further,” says Aiello. “There’s going to be more need for skilled workers in all different types of areas and more people pulling workers from all different areas to come into manufacturing.”
Different Pipelines into Advanced Automation Manufacturing Careers
FANUC America’s network of schools is already training many young people every year. In addition to attracting traditional students, the company also has different channels for accessing people of different backgrounds and funneling them into a promising manufacturing career.
“We have robots in four U.S. military bases. So, for those departing the service, they can go into robotics and/or CNC training programs, or even get hired right out of the military,” says Aiello. “We know that our customers love to hire people out of the military because of the discipline and real-world experience they’ve attained while serving.”
For those coming out of the military, FANUC America has a transition assistance program to prepare them for civilian careers. FANUC America also provides veteran training programs, named Workshops for Warriors, for military personnel that have been out of the service.
“Another path to manufacturing careers we’ve created is for returning citizens that have been incarcerated,” says Aiello. “In these programs, people have the ability to gain skills that prepares them for viable manufacturing jobs.”
Studies show worker training programs for previously incarcerated people greatly reduce the rate of recidivism. Moreover, these programs build skills that can help them find rewarding careers in manufacturing.
FANUC America also has many community-based programs, such as FOCUS Hope in Detroit, Michigan, which reaches underserved and underrepresented areas. These efforts are part of the Workforce Innovation and Opportunity Act, designed to strengthen and improve America’s workforce system by helping Americans, including youth and those with barriers to employment, attain high-quality jobs.
“These programs are focused on reaching and addressing a very diverse population and allowing them to train and then land good manufacturing jobs,” says Aiello.
How FANUC America is a Key Part of the Manufacturing Workforce Solution
With the level of advanced automation increasing and expanding in the industry, the need for skilled labor is real. Additionally, these new manufacturing jobs offer solid starting salaries, typically, around $60,000 annually, and require little more than one year of post-secondary education. Frequently, this education is free due to many employers paying tuition reimbursement.
“I don’t know too many other jobs that can provide a great living wage and a career path,” says Aiello. “In no other area than in manufacturing can you obtain a good, high-paying job for much less educational investment.”
Recently, FANUC America and Rockwell Automation officially formed a coalition to create apprenticeship programs designed to upskill current and future workers for jobs in advanced manufacturing, robotics and automation.
“FANUC America is uniquely positioned to engage and rally policymakers as well as work with our industry partners to leverage the education network and utilize our own internal training in the FANUC Academy,” says Aiello. “Never before has there been a willingness to bring all this together. So, what employers really need to focus on in the coming years is how they will develop their workforce.”
Because FANUC America works with manufacturers of all sectors across the industry, from food and beverage to automotive to aerospace to medical, not only can its training solutions help create skilled production and manufacturing workers, but also engineering staff.
These new manufacturing jobs offer solid starting salaries, typically, around $60,000 annually, and require little more than one year of post-secondary education.
“People going into engineering need to have an understanding of the technology that’s being deployed,” he says. “We have an infrastructure in place to train this through the FANUC Academies and through our direct educational partnerships.”
FANUC America continues to develop training solutions, such as helping students understand process controls, analytics and Ethernet communication. This is important because when more manufacturing comes back to the U.S., the jobs will likely look different than they did decades ago. Manufacturers will have two choices: upskill or hire workers with the right skills.
“As an employer that’s a challenge, but FANUC America is a part of the solution,” says Aiello. Stay tuned next week to receive the 5th edition of our 5 part series on developing the future of manufacturing skills.